Kalibraatio vs. Verification: What You Need to Know
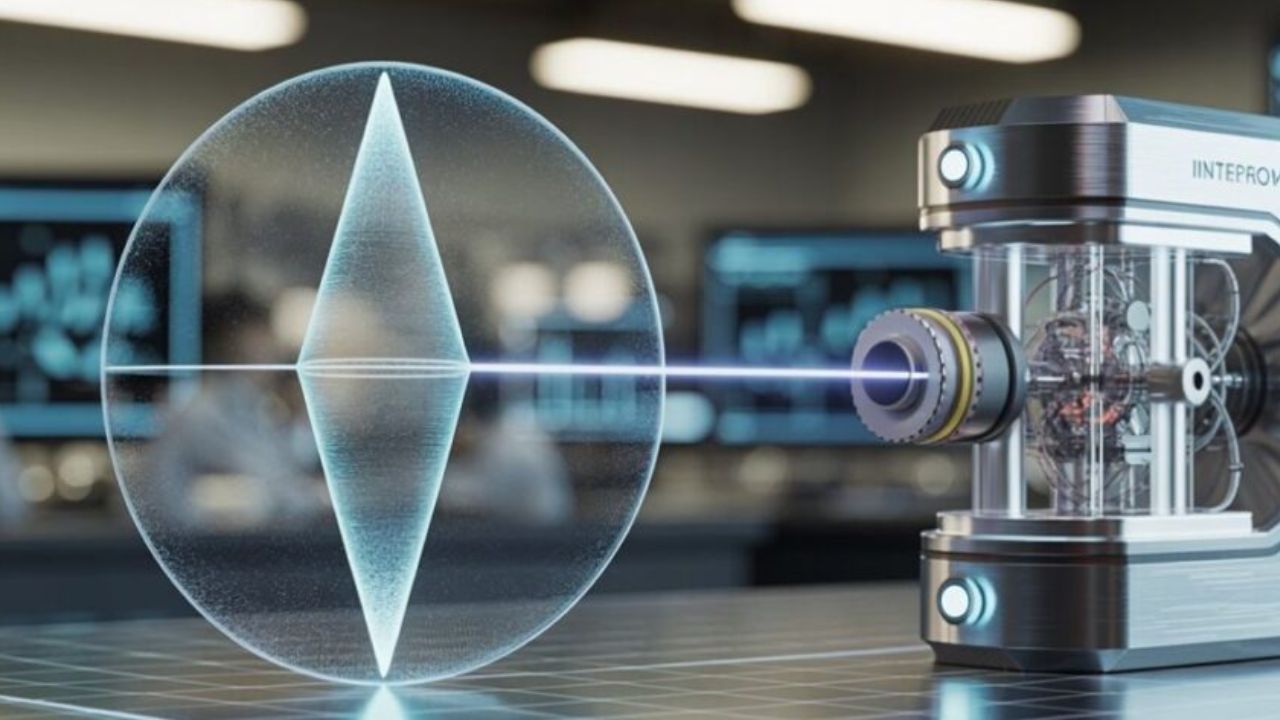
When it comes to precision and accuracy, two terms often come up in discussions: kalibraatio and verification. While they may sound similar, they serve distinct purposes that can significantly impact your measurements. Whether you’re working in a lab, manufacturing setting, or any field where precise data is crucial, understanding the difference between these processes is essential. In this blog post, we’ll delve into what kalibraatio and verification really mean, why accurate measurements matter, and how to choose the right method for your specific needs. Get ready to enhance your knowledge of measurement reliability!
Understanding Calibration and Verification
Calibration and verification are critical concepts in the world of measurement. Calibration refers to the process of adjusting an instrument or tool to ensure its accuracy against a known standard. This may involve comparing measurements taken by your device with those from a reference source, then making necessary adjustments.
Verification, on the other hand, is about confirming that an instrument meets specified requirements without necessarily altering it. It ensures that your equipment performs within acceptable limits as defined by industry standards or regulations.
While both processes aim for precision, they approach this goal differently. Understanding these distinctions can help professionals select the right method for their specific applications and maintain high-quality data integrity in their work. Each plays a vital role in ensuring reliability across various fields—from engineering to laboratory settings—where accurate measurements are non-negotiable.
The Importance of Accurate Measurements
Accurate measurements are vital across various industries. They ensure that products meet safety standards and function as intended. In manufacturing, even the slightest deviation can lead to failures or recalls.
In scientific research, precise data collection is crucial for valid results. Researchers rely on accurate measurements to draw meaningful conclusions and advance knowledge in their fields.
Healthcare also hinges on exactness. Medication dosages must be administered correctly to avoid harmful effects or ineffective treatment.
Moreover, businesses experience a direct impact on profitability due to measurement accuracy. Errors can result in wasted resources and lost time, ultimately harming the bottom line.
With globalization increasing competition, maintaining high standards of precision becomes essential for success. Embracing robust calibration practices helps organizations build trust with customers while enhancing overall efficiency.
Differences Between Kalibraatio and Verification
Kalibraatio and verification are often confused, but they serve distinct purposes in measurement accuracy. Kalibraatio refers to the process of adjusting instruments so they provide accurate readings against a known standard. It ensures that your tools can deliver precise results.
Verification, on the other hand, involves checking whether an instrument meets specified requirements or standards. This process confirms that measurements fall within acceptable limits but does not adjust the equipment itself.
Another key difference lies in frequency and application. Kalibraatio is typically performed periodically based on usage or environmental factors, while verification might occur more frequently as part of routine checks to maintain compliance.
Understanding these differences helps businesses implement effective quality control measures tailored to their specific needs and regulatory requirements.
The Kalibraatio Process
Kalibraatio is a meticulous process that ensures instruments produce accurate and reliable results. It begins with selecting the right reference standards. These are usually traceable to national or international measurements.
Next, the instrument in question is examined under controlled conditions. This could involve adjusting settings or replacing components to align it with the established standard.
After adjustments, multiple tests are conducted to confirm accuracy across various ranges of measurement. Each test generates data that reflects how well the instrument meets specifications.
Once calibration is complete, detailed documentation is prepared. This record includes before-and-after results and any adjustments made during the process.
Regular follow-ups are essential for maintaining accuracy over time. Routine checks help identify drift or deviations that may occur due to wear or environmental factors.
The Verification Process
The verification process is crucial for ensuring that instruments and systems operate correctly. This step often follows calibration, confirming that the measurements taken are consistent with established standards.
During verification, you assess whether an instrument performs as intended under specific conditions. It’s about checking functionality rather than adjusting it.
Typically, this involves comparing the output of your device against a known reference or standard. Any discrepancies must be noted and addressed immediately to maintain reliability.
Verifying equipment can occur in various environments—laboratories, manufacturing floors, or fieldwork settings. The context influences how rigorous the checks need to be.
Documentation plays a vital role here; maintaining records of each verification helps track performance over time and supports regulatory compliance when necessary.
Choosing the Right Method for Your Needs
Choosing between kalibraatio and verification can be tricky. Each method serves distinct purposes, so understanding your needs is vital.
If precision in measurements is essential for your project, kalibraatio might be the better choice. It ensures that instruments are functioning accurately according to established standards. This process can significantly reduce errors in critical applications like laboratory research or manufacturing.
On the other hand, if you need to confirm that a device meets certain specifications without recalibrating it, verification could suffice. This method provides assurance that equipment operates within acceptable limits but doesn’t adjust its accuracy.
Consider factors such as industry regulations, budget constraints, and time availability when making a decision. Your specific requirements will dictate which approach aligns best with your goals and resources.